Solar Charge Controller: Introduction
- Michelle
- Mar 7, 2020
- 8 min read
A charge controller is an essential part of nearly all power systems that charge batteries, whether the power source is PV, wind, hydro, fuel, or utility grid. Its purpose is to keep your batteries properly fed and safe for the long term.
The basic functions of a controller are quite simple. Charge controllers block reverse current and prevent battery overcharge. Some controllers also prevent battery over discharge, protect from electrical overload, and/or display battery status and the flow of power. Let's examine each function individually.
Blocking Reverse Current
Photovoltaic panels work by pumping current through your battery in one direction. At night, the panels may pass a bit of current in the reverse direction, causing a slight discharge from the battery. (Our term "battery" represents either a single battery or bank of batteries.) The potential loss is minor, but it is easy to prevent. Some types of wind and hydro generators also draw reverse current when they stop (most do not except under fault conditions).
In most controllers, charge current passes through a semiconductor (a transistor) which acts like a valve to control the current. It is called a "semiconductor" because it passes current only in one direction. It prevents reverse current without any extra effort or cost.
In some controllers, an electromagnetic coil opens and closes a mechanical switch. This is called a relay. (You can hear it click on and off.) The relay switches off at night, to block reverse current.
If you are using a PV array only to trickle-charge a battery (a very small array relative to the size of the battery), then you may not need a charge controller. This is a rare application. An example is a tiny maintenance module that prevents battery discharge in a parked vehicle but will not support significant loads. You can install a simple diode in that case, to block reverse current. A diode used for this purpose is called a "blocking diode."
Preventing Overcharge
When a battery reaches full charge, it can no longer store incoming energy. If energy continues to be applied at the full rate, the battery voltage gets too high. Water separates into hydrogen and oxygen and bubbles out rapidly. (It looks like it's boiling so we sometimes call it that, although it's not actually hot.) There is excessive loss of water, and a chance that the gasses can ignite and cause a small explosion. The battery will also degrade rapidly and may possibly overheat. Excessive voltage can also stress your loads (lights, appliances, etc.) or cause your inverter to shut off.
Preventing overcharge is simply a matter of reducing the flow of energy to the battery when the battery reaches a specific voltage. When the voltage drops due to lower sun intensity or an increase in electrical usage, the controller again allows the maximum possible charge. This is called "voltage regulating." It is the most essential function of all charge controllers. The controller "looks at" the voltage, and regulates the battery charging in response.
Some controllers regulate the flow of energy to the battery by switching the current fully on or fully off. This is called "on/off control." Others reduce the current gradually. This is called "pulse width modulation" (PWM). Both methods work well when set properly for your type of battery.
A PWM controller holds the voltage more constant. If it has two-stage regulation, it will first hold the voltage to a safe maximum for the battery to reach full charge. Then, it will drop the voltage lower, to sustain a "finish" or "trickle" charge. Two-stage regulating is important for a system that may experience many days or weeks of excess energy (or little use of energy). It maintains a full charge but minimizes water loss and stress.
The voltages at which the controller changes the charge rate are called set points. When determining the ideal set points, there is some compromise between charging quickly before the sun goes down, and mildly overcharging the battery. The determination of set points depends on the anticipated patterns of usage, the type of battery, and to some extent, the experience and philosophy of the system designer or operator. Some controllers have adjustable set points, while others do not.
Control Set Points vs. Temperature
The ideal set points for charge control vary with a battery's temperature. Some controllers have a feature called "temperature compensation." When the controller senses a low battery temperature, it will raise the set points. Otherwise when the battery is cold, it will reduce the charge too soon. If your batteries are exposed to temperature swings greater than about 30° F (17° C), compensation is essential.
Some controllers have a temperature sensor built in. Such a controller must be mounted in a place where the temperature is close to that of the batteries. Better controllers have a remote temperature probe, on a small cable. The probe should be attached directly to a battery in order to report its temperature to the controller.
An alternative to automatic temperature compensation is to manually adjust the set points (if possible) according to the seasons. It may be sufficient to do this only twice a year, in spring and fall.
Control Set Points vs. Battery Type
The ideal set points for charge controlling depend on the design of the battery. The vast majority of solar power systems use deep-cycle lead-acid batteries of either the flooded type or the sealed type. Flooded batteries are filled with liquid. These are the standard, economical deep cycle batteries.
Sealed batteries use saturated pads between the plates. They are also called "valve-regulated" or "absorbed glass mat," or simply "maintenance-free." They need to be regulated to a slightly lower voltage than flooded batteries or they will dry out and be ruined. Some controllers have a means to select the type of battery. Never use a controller that is not intended for your type of battery.
Typical Set Points For 12V Lead-Acid Batteries at 77°F (25°C)
(These are typical, presented here only for example.)
High limit (flooded battery): 14.4 V
High limit (sealed battery): 14.0 V
Resume full charge: 13.0 V
Low voltage disconnect: 10.8 V
Reconnect: 12.5 V
Temperature compensation for 12V battery: -0.03 V per ° C deviation from standard 25° C
Low Voltage Disconnect (LVD)
The deep-cycle batteries used in renewable energy systems are designed to be discharged by about 80%. If they are discharged 100%, they are immediately damaged. Imagine a pot of water boiling on your kitchen stove. The moment it runs dry, the pot overheats. If you wait until the steaming stops, it is already too late!
Similarly, if you wait until your lights look dim, some battery damage will have already occurred. Every time this happens, both the capacity and the life of the battery will be reduced by a small amount. If the battery sits in this over discharged state for days or weeks at a time, it can be ruined quickly.
The only way to prevent over discharge when all else fails, is to disconnect loads (appliances, lights, etc.), and then to reconnect them only when the voltage has recovered due to some substantial charging. When over discharge is approaching, a 12V battery drops below 11V (a 24 V battery drops below 22 V).
A low voltage disconnect circuit will disconnect loads at that set point. It will reconnect the loads only when the battery voltage has substantially recovered due to the accumulation of some charge. A typical LVD reset point is 13V (26 V on a 24 V system).
All modern dc power inverters have LVD built in, even cheap pocket-sized ones. The inverter will turn off to protect itself and your loads as well as your battery. Normally, an inverter is connected directly to the batteries, not through the charge controller, because its current draw can be very high, and because it does not require external LVD.
If you have any DC loads, you should have an LVD. Some charge controllers have one built in. You can also obtain a separate LVD device. Some LVD systems have a "mercy switch" to let you draw a minimal amount of energy, at least long enough to find the candles and matches! DC refrigerators have LVD built in.
If you purchase a charge controller with built-in LVD, make sure that it has enough capacity to handle your DC loads. For example, let's say you need a charge controller to handle less than 10A of charge current, but you have a DC water pressurizing pump that draws 20A (for short periods) plus a 6A DC lighting load. A charge controller with a 30A LVD would be appropriate. Don't buy a 10A charge controller that has only a 10A or 15A load capacity!
Overload Protection
A circuit is overloaded when the current flowing in it is higher than it can safely handle. This can cause overheating and can even be a fire hazard. Overload can be caused by a fault (short circuit) in the wiring, or by a faulty appliance (like a frozen water pump). Some charge controllers have overload protection built in, usually with a push-button reset.
Built-in overload protection can be useful, but most systems require additional protection in the form of fuses or circuit breakers. If you have a circuit with a wire size for which the safe carrying capacity is less than the overload limit of the controller, then you must protect that circuit with a fuse or breaker of a suitably lower Amp rating. In any case, follow the manufacturer's requirements for any external fuse or circuit breaker requirements.
Displays and Metering
Charge controllers include a variety of possible displays, ranging from a single red light to digital displays of voltage and current. These indicators are important and useful. Imagine driving across the country with no instrument panel in your car! A display system can indicate the flow of power into and out of the system, the approximate state of charge of your battery, and when various limits are reached.
If you want to complete and accurate monitoring however, spend about S$200 for a separate digital device that includes an Amp-hour meter. It acts like an electronic accountant to keep track of the energy available in your battery. If you have a separate system monitor, then it is not important to have digital displays in the charge controller itself. Even the cheapest system should include a voltmeter as a bare minimum indicator of system function and status.
Have It All with a Power Center
If you are installing a system to power a modern home, then you will need safety shutoffs and interconnections to handle high current. The electrical hardware can be bulky, expensive and laborious to install. To make things economical and compact, obtain a ready-built power center. It can include a charge controller with LVD and digital monitoring as options. This makes it easy for an electrician to tie in the major system components, and to meet the safety requirements of the local authorities.
Charge Controllers for Wind and Hydro
A charge controller for a wind-electric or hydro-electric charging system must protect batteries from overcharge, just like a PV controller. However, a load must be kept on the generator at all times to prevent the turbine from over-speeding. Instead of disconnecting the generator from the battery (like most PV controllers) it diverts excess energy to a special load that absorbs most of the power from the generator. That load is usually a heating element, which "burns off" excess energy as heat. If you can put the heat to good use, fine!
Is It Working?
How do you know if a controller is malfunctioning? Watch your voltmeter as the batteries reach full charge. Is the voltage reaching (but not exceeding) the appropriate set points for your type of battery? Use your ears and eyes-are the batteries bubbling severely? Is there a lot of moisture accumulation on the battery tops? These are signs of possible overcharge. Are you getting the capacity that you expect from your battery bank? If not, there may be a problem with your controller, and it may be damaging your batteries.
Conclusion
The control of battery charging is so important that most manufacturers of high quality batteries (with warranties of five years or longer) specify the requirements for voltage regulation, low voltage disconnect and temperature compensation. When these limits are not respected, it is common for batteries to fail after less than one quarter of their normal life expectancy, regardless of their quality or their cost.
A good charge controller is not expensive in relation to the total cost of a power system. Nor is it very mysterious. I hope this article has given you the background that you need to make a good choice of controls for your power system.
At Solar Era, we will be happy to help find the products that are right for you. For pricing and product information give us a call. We'll also answer any questions you might have about your system.
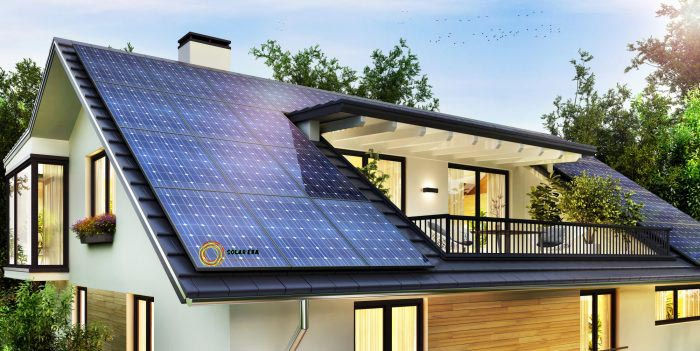
Comments